Introduction:
Heat exchangers are an essential component in various industrial processes, and they come in different types and designs. One of the most popular types of heat exchangers is the finned tube. Finned tubes enhance heat transfer by increasing the surface area between the fluid inside the tube and the surrounding environment. In this comprehensive guide, we will explore the eight different types of heat exchanger finned tubes, their characteristics, applications, and advantages.

Type 1: Plain Fin Tube
Plain fin tubes are the simplest and most commonly used type of heat exchanger finned tubes. They consist of a bare tube with external fins attached to it. The fins increase the surface area of the tube, which results in better heat transfer. Plain fin tubes are suitable for low to medium heat transfer applications and are commonly used in air coolers, air heaters, and economizers.

Type 2: Extruded Fin Tube
Extruded fin tubes are produced by extruding fins from the wall of a plain tube. Extruded fins have higher thermal conductivity and are more robust than plain fins, making them suitable for high-temperature and high-pressure applications. They are commonly used in heat recovery steam generators, boilers, and superheaters.
Type 3: Embedded Fin Tube
Embedded fin tubes have fins that are embedded into the wall of the tube. This type of finned tube has excellent heat transfer characteristics and is ideal for high-temperature and high-pressure applications. Embedded fin tubes are commonly used in heat exchangers for the oil and gas industry, chemical processing, and power generation.
Type 4: Spiral Fin Tube
Spiral fin tubes have fins that are wound in a spiral around the tube. This design increases the surface area of the tube, resulting in better heat transfer. Spiral fin tubes are suitable for low to medium heat transfer applications and are commonly used in air-cooled heat exchangers and air-cooled condensers.
Type 5: Longitudinal Fin Tube
Longitudinal fin tubes have fins that run parallel to the tube’s axis. This design results in a more compact heat exchanger with higher heat transfer rates. Longitudinal fin tubes are commonly used in air-cooled heat exchangers and air-cooled condensers.
Type 6: Internally Finned Tube
Internally finned tubes have fins on the inside of the tube. This design is suitable for high-temperature and high-pressure applications, and the fins increase the surface area of the tube for better heat transfer. Internally finned tubes are commonly used in heat exchangers for the oil and gas industry, chemical processing, and power generation.
Type 7: Low Fin Tube
Low fin tubes have fins that are lower in height than other types of fins, resulting in a more compact heat exchanger. Low fin tubes have higher heat transfer rates than plain fin tubes and are suitable for applications where space is limited. Low fin tubes are commonly used in air-cooled heat exchangers, air-cooled condensers, and compact heat exchangers.
Type 8: Herringbone Fin Tube
Herringbone fin tubes have fins that are arranged in a herringbone pattern, resulting in a more compact heat exchanger with higher heat transfer rates. Herringbone fin tubes are suitable for low to medium heat transfer applications and are commonly used in air-cooled heat exchangers and air-cooled condensers.
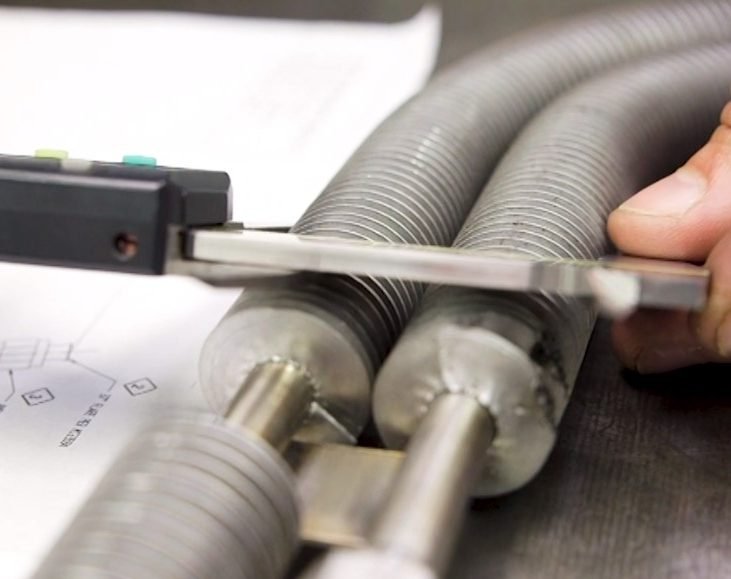
Conclusion:
Finned tubes are an essential component in heat exchangers, and choosing the right type of finned tube for an application is critical. Each type of finned tube has its unique characteristics, advantages, and disadvantages. In this comprehensive guide, we have explored the eight